Tool Cutting-Face Materials
Cutting-tool performance hinges critically on the face material. High-Speed Steel (HSS) remains popular for its toughness and affordability. Cemented carbides deliver a balance of hardness and toughness for high-volume machining. Tungsten-carbide tips boost insert life under abrasive conditions. Polycrystalline Diamond (PCD) excels on nonferrous and composite materials, while Cubic Boron Nitride (CBN) dominates ferrous and hardened alloys. Ceramic inserts shine in high-speed, high-temperature cutting of super-alloys. Cermets combine metal toughness with ceramic hardness, excelling in finishing operations.
Each material has its sweet spot in terms of cost, cutting speed, temperature resistance, and workpiece compatibility—understanding these trade-offs helps select the optimal tool for any application.
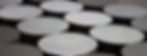
High-Speed Steel (HSS)
High-Speed Steel was the first truly high-performance cutting tool alloy, offering a good balance of wear resistance and toughness.
Composition & Hardness: Typically M2 or M42 grades, hardened to ~62 HRC through austenitizing, quenching, and tempering processes.
Temperature Resistance: Operates up to 600–620 °C without losing hardness.
Advantages:
High impact resistance; ideal for interrupted cuts
Lower cost; well-suited to “high-mix, low-volume” runs
Limitations:
Lower hot hardness than carbides (max ~30 m/min cutting speed)
Faster wear in high-speed, high-volume applications
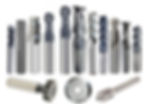
Solid Carbide
Cemented (tungsten) carbide tools consist of fine WC particles held in a cobalt matrix, offering superior hardness and wear resistance.
Grades: Common substrate WC-6Co to WC-10Co-4Cr; coatings (TiN, TiAlN, TiCN) are often applied via CVD or PVD.
Properties:
Hardness up to ~1,600 HV
Good fracture toughness; higher hot hardness than HSS
Applications: General-purpose turning, milling, drilling at medium to high speeds
Advantages:
Outstanding wear resistance in abrasive conditions
Excellent dimensional stability
Limitations:
More brittle than HSS; sensitive to shock
Higher cost per insert
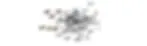
Tungsten-Carbide Tips
Often employed as replaceable tips welded onto tool bodies, tungsten-carbide tips leverage carbide’s wear resistance while minimizing tooling costs.
Typical Use: Road-planing picks, mining and construction bits, wood-cutting saw tips.
Benefits:
Rapid tip replacement lowers downtime
Carbide tip hardness (>1,200 HV) resists abrasive wear
Trade-offs:
Joint between tip and body can be a stress-concentration site
Limited shock resistance compared to solid carbide tools

Polycrystalline Diamond (PCD)
PCD tools feature a synthetic diamond cutting layer sintered onto a carbide substrate.
Structure: 90–95% diamond particles bonded with a cobalt metal matrix under extreme pressure and temperature.
Applications:
Nonferrous metals (aluminum, brass)
Composites (MDF, fiber-reinforced plastics, carbon composites)
Wood and paper products
Advantages:
Unmatched abrasion resistance; tool life up to 100× carbide.
Produces exceptionally fine surface finishes
Limitations:
Cannot machine ferrous alloys (chemical wear)
High upfront cost
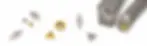
Cubic Boron Nitride (CBN)
CBN is the second-hardest material after diamond, tailored for ferrous and hardened alloys.
Forms: Polycrystalline CBN (PCBN) inserts or mixed CBN/ceramic grades.
Applications:
Hardened steels (>45 HRC), cast irons, superalloys
High-precision finishing and form turning
Advantages:
Exceptional hot hardness and thermal stability
High chemical inertness; resists diffusion wear up to 1,000 °C
Limitations:
High cost limits use to specialized applications
Requires rigid setups due to brittleness
Ceramic Inserts
Advanced ceramics (silicon nitride, alumina, SiC whisker-reinforced) excel at very high speeds and temperatures.
Grades: SPK®, SECOMAX™, and others, often optimized for superalloys and hardened steels.
Properties:
Hardness ~1,800 HV; stable to 1,200 °C
Low thermal expansion; maintains cutting edge at high speeds
Applications:
High-speed finishing of Inconel, titanium, stainless steels
Advantages:
Superior wear resistance at >500 m/min cutting speeds
Longer tool life than uncoated carbide
Limitations:
Very low fracture toughness; susceptible to shock
Requires CNC machines with precise control
Cermet Grades
Cermets blend metal binders with ceramic particles (TiC, TiN) to combine toughness with high-temperature hardness.
Characteristics:
Better wear resistance than HSS, better toughness than ceramics
Ideal for fine finishing at moderate speeds
Applications:
Precision turning where surface finish and dimensional accuracy are paramount
Trade-offs:
Lower thermal stability than pure ceramics or CBN
Typically more expensive than carbide
Comparison
Technical specification
Material | Hardness | Toughness | Max Temp (°C) | Speed (m/min) | Cost Index | Applications |
HSS | ~700 HV / 62 HRC | High | 600–620 | 20–30 | Low | Interrupted cuts, general purpose |
Cemented Carbide | 1 200–1 600 HV | Medium | 900 | 100–300 | Medium | High-volume turning, milling |
Tungsten-Carbide Tips | ~1 200 HV | Medium | 900 | 80–200 | Low–Med | Mining, road-planing, saw tips |
PCD | >10 000 HV (diamond) | Low | 800 | 500–1 000 | High | Nonferrous, composites, wood |
CBN | ~4 500 HV | Very Low | 1 000 | 200–400 | Very High | Hardened steels, cast irons |
Ceramics | ~1 800 HV | Very Low | 1 200 | 300–600 | High | Super-alloys, high-speed finishing |
Cermets | ~1 400 HV | Low–Med | 700–800 | 100–200 | Medium | Precision turning, fine finishing |
Application Suitability
Material | Ferrous | Non-ferrous | Composites | Abrasive | Interrupted | High-temp |
HSS | ✓ | ✓ | – | – | ✓ | – |
Carbide | ✓ | ✓ | ✓ | ✓ | – | – |
PCD | – | ✓ | ✓ | ✓ | – | – |
CBN | ✓ | – | – | ✓ | ✓ | ✓ |
Ceramics | ✓ | – | – | ✓ | – | ✓ |
Cermets | ✓ | ✓ | – | – | ✓ | – |
Selecting the right cutting-tool face material is the final piece in maximizing your machining efficiency, part quality, and overall profitability. Whether you’re running high-volume steel production with carbide, achieving microscopic tolerances on hardened alloys with CBN, or tackling composites and aluminum with PCD, each material offers a unique balance of hardness, toughness, temperature resistance, and cost. By leveraging the comparison tables and visual guides provided, you can confidently match tool grades to your specific application, reduce downtime, and extend tool life.
Contact our technical sales team today for personalized recommendations, free sample trials, and expert support tailored to your shop’s exact needs. Let’s cut smarter together!
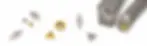